Erfolg war schon immer eine Frage richtiger Entscheidungen.
Unsere Zertifizierungen im Bereich
Qualitätsmanagement und Bildung
Unsere Zertifikate
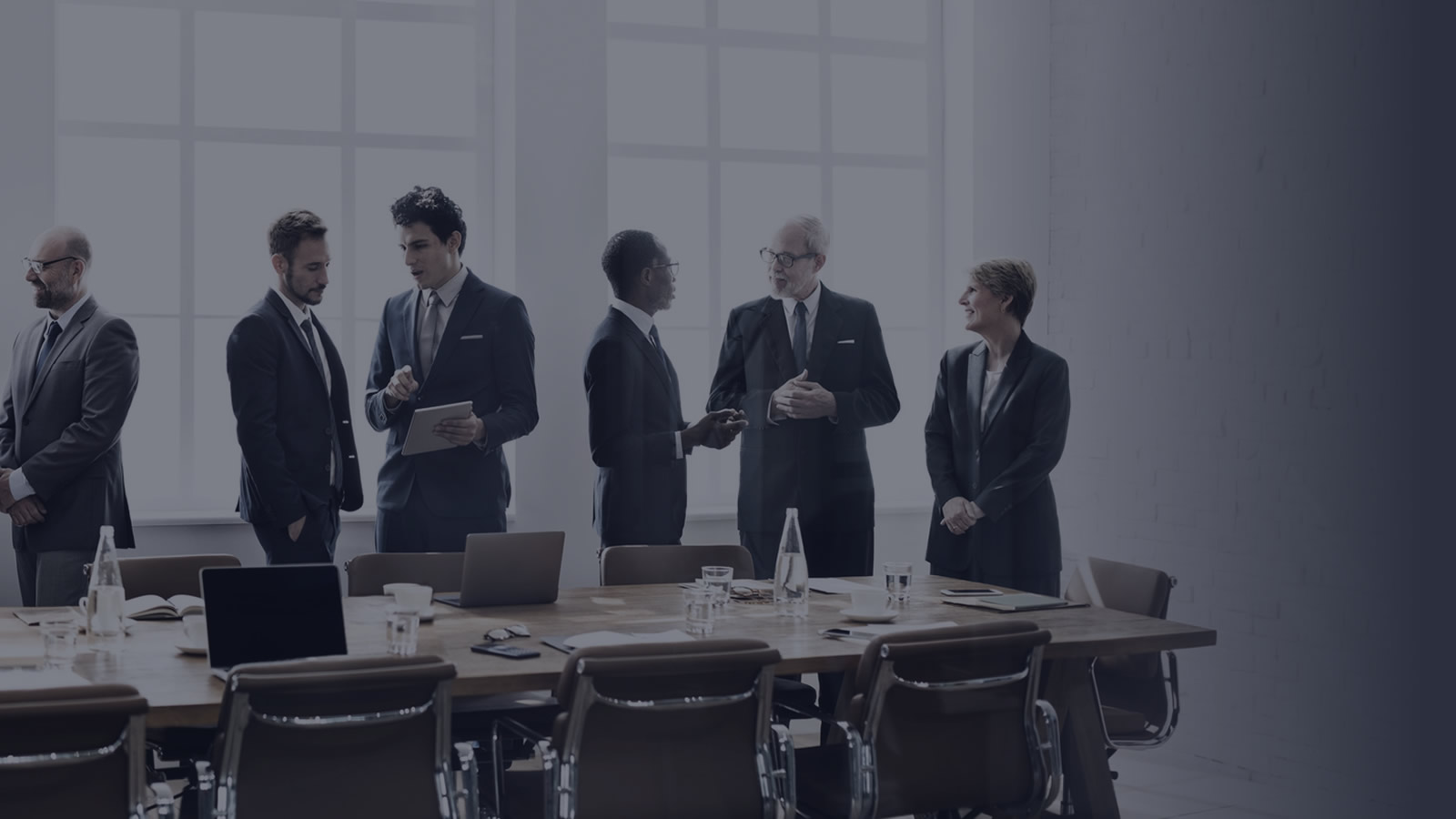
ISO 9001
Die internationale Norm beschreibt Anforderungen an Qualitätsmanagement-Systeme.
Unsere Zertifizierungen im Bereich
Qualitätsmanagement und Bildung
AZAV
Die AZAV beschreibt Voraussetzungen zur Zulassung von Trägern und Maßnahmen der Arbeitsförderung nach SGB III.
Wer höchste Standards hält, sollte diese auch zertifizieren lassen.
Unsere Zertifizierungen im Bereich
Umwelt und Energie
Unsere Zertifikate
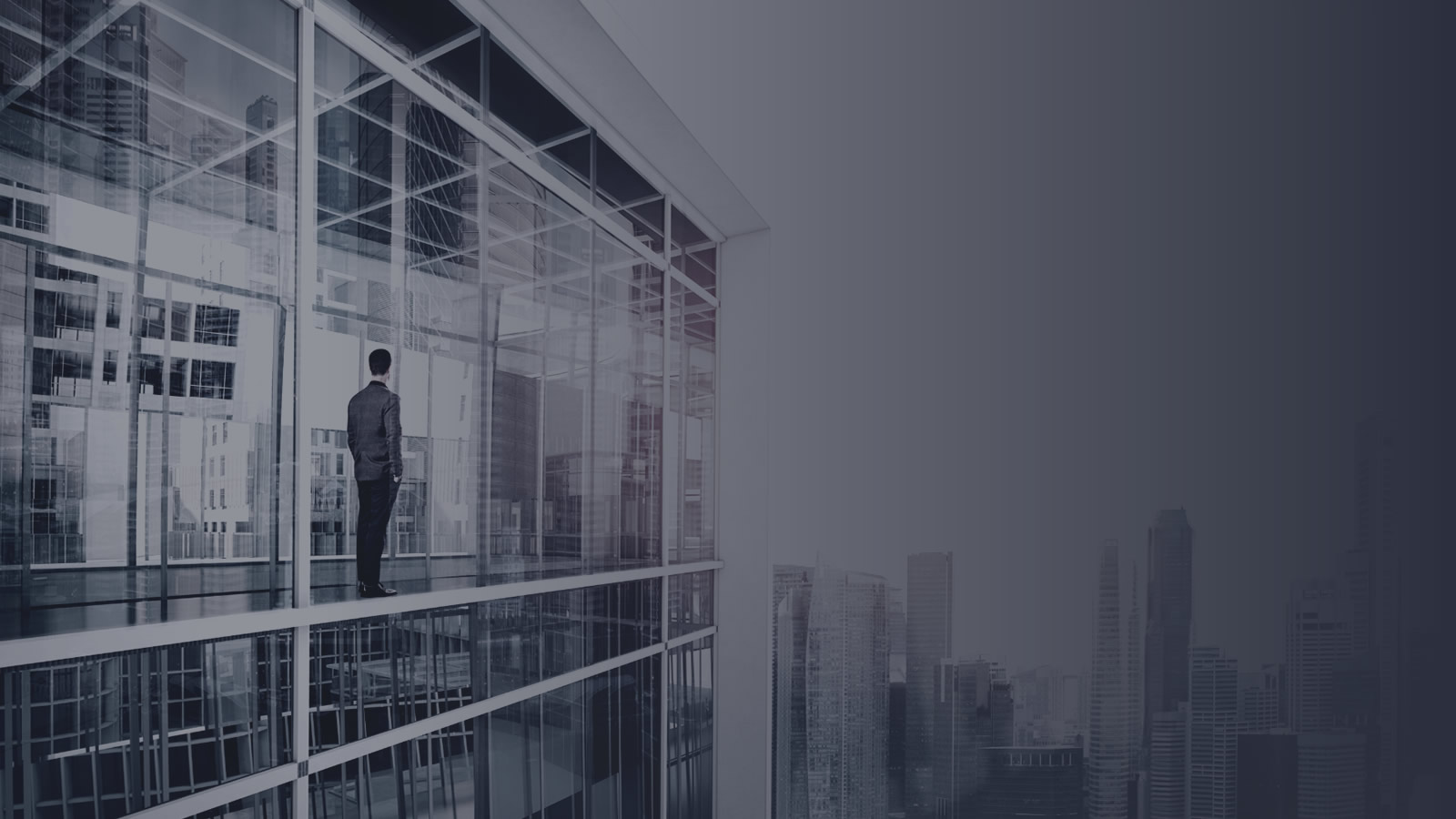
ISO 14001
Die internationale Norm beschreibt Anforderungen an Umweltmanagement-Systeme.
Unsere Zertifizierungen im Bereich
Umwelt und Energie
ISO 50001
Die internationale Norm legt Anforderungen an ein Energiemanagement-System fest.
Arbeitsschutz steigert Ihren Unternehmens-Erfolg
Unsere Zertifizierungen im Bereich
Arbeitssicherheit
Unsere Zertifikate
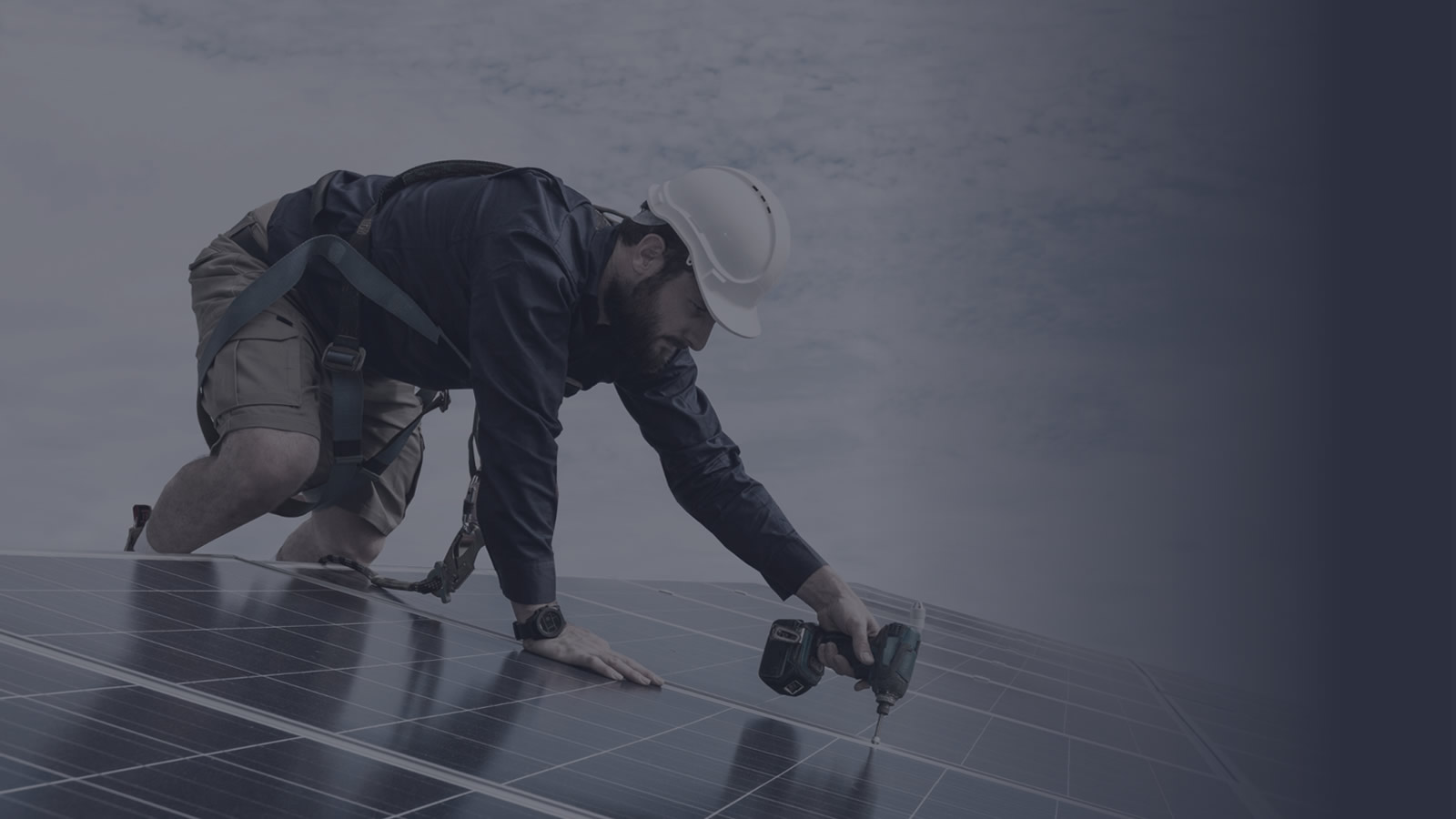
SCC/SCP
SCC ist vor vielen Jahren in der petrochemischen Industrie entwickelt worden.
Unsere Zertifizierungen im Bereich
Arbeitssicherheit
ISO 45001
Der Standard für Management-Systeme für Sicherheit und Gesundheit bei der Arbeit
Sicherheit lässt sich nicht kaufen – aber zertifizieren.
Unsere Zertifizierungen im Bereich
Sicherheits-Dienstleistungen
Unsere Zertifikate
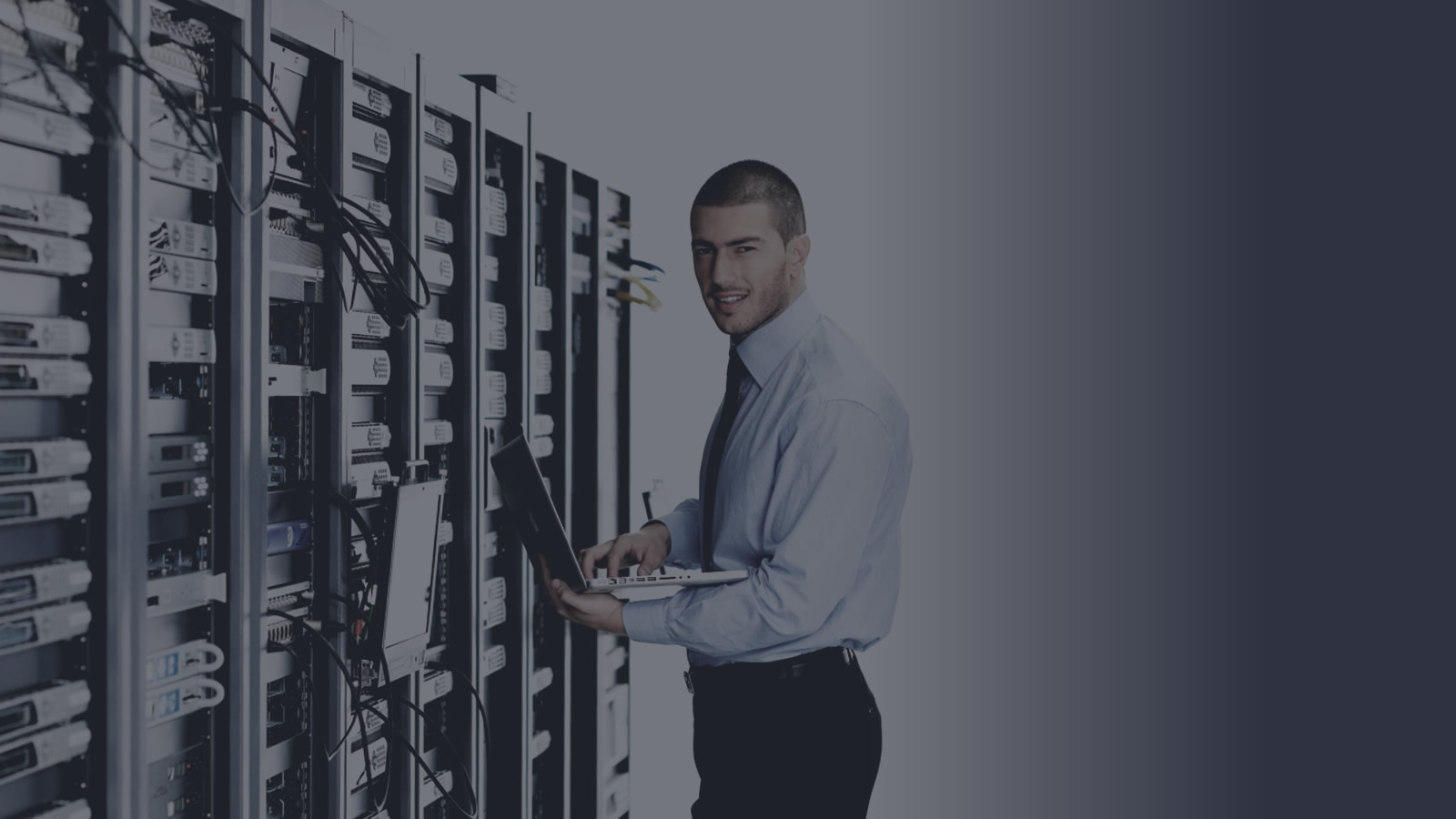
ISO 77200-1
Die DIN 77200-1 gilt für stationäre und mobile Sicherheits-Dienstleistungen sowie den Veranstaltungssicherungsdienst.
Die DIN 77200-Reihe beschreibt allgemeine Anforderungen an Sicherheits-Dienstleister und deren Zertifizierung.
Herzlich willkommen bei der ICG Zertifizierung GmbH. Als eine von der Deutschen Akkreditierungsstelle DAkkS GmbH zugelassene Konformitätsbewertungsstelle bieten wir die Zertifizierung von Managementsystemen, Produkten und Dienstleistungen an. Bundesweit vertreten sind wir immer da, wo Sie uns brauchen.
30.03.2022 Neuer Kundenbereich auf unserer Internetseite
Für unsere Kunden haben wir hier einen neuen passwortgeschützen Bereich angelegt. Hier finden Sie unter anderem
- Meldelisten und Antragsformulare,
- Fragebogen zur Kundenzufriedenheit,
- Beschreibung zu unserem Einspruchsverfahren (neu),
- Informationen zu erfolgten Änderungen in div. Dokumenten (neu).
Unser Zertifizierungsprogramm im Überblick
Qualitätsmanagement
Die internationale Norm ISO 9001:2015 beschreibt Anforderungen an Qualitätsmanagement-Systeme. Weltweit nutzen Unternehmen die Norm ISO 9001 als Instrument / Grundlage zur Steuerung Ihres Unternehmens sowie zur Verbesserung Ihrer Leistungsfähigkeit. Somit ist die ISO 9001 seit vielen Jahren in verschiedensten Organisationen als ein entscheidendes „Lenkungsinstrument“ etabliert. Am weitesten verbreitet ist die ISO 9001 in industriell tätigen Unternehmen, da sie hier Ihren Ursprung hatte.
mehr erfahrenAZAV
TermineZulassung von Trägern und Maßnahmen der Arbeitsförderung nach SGB III
Die in der Akkreditierungs- und Zulassungsverordnung Arbeitsförderung (AZAV) enthaltenen Regelungen zur Zulassung von Trägern und Maßnahmen der Arbeitsförderung nach dem SGB III verfolgen das Ziel, die Qualität arbeitsmarktlicher Dienstleistungen und damit Leistungsfähigkeit und Effizienz des arbeitsmarktpolitischen Fördersystems nachhaltig sicherzustellen. Die AZAV-Träger- und Maßnahmezulassung ist die Voraussetzung für Bildungseinrichtungen, um von der Bundesagentur für Arbeit an arbeitsuchende Personen ausgegebene Bildungsgutscheine oder Aktivierungs- und Vermittlungsgutscheine (AVGS) einzulösen.
mehr erfahrenISO 14001
TermineUmweltmanagement
Die internationale Norm ISO 14001:2015 beschreibt Anforderungen an Umweltmanagement-Systeme. Weltweit nutzen Unternehmen die Norm ISO 14001 als Werkzeug zur Steuerung Ihres Unternehmens unter dem Aspekt des nachhaltigen Umganges mit den natürlichen Ressourcen sowie der kontinuierlichen Verbesserung ihrer Umweltleistung.
mehr erfahrenISO 50001
TermineEnergiemanagement
Die internationale Norm ISO 50001 legt Anforderungen an ein Energiemanagementsystem fest. Sie ist damit die erste weltweit gültige Norm zur Zertifizierung von Energiemanagementsystemen (EnMS), welche im Dezember 2011 veröffentlicht wurde. Damit ersetzt sie DIN EN 16001, welche bis dahin als deutsche / europäische Norm für EnMS angewandt wurde.
mehr erfahrenVAZ-SCC
TermineArbeitssicherheit
Die Zertifizierung nach SCC (Sicherheits Certifikat Contraktoren) ist vor vielen Jahren in der petrochemischen Industrie entwickelt worden. Ein zertifiziertes Managementsystem ist heute für viele Unternehmen ein Nachweis für ein angewandtes SGU (Sicherheit, Gesundheit, Umweltschutz)-System für den Einsatz in verschiedenen Industriebereichen.
mehr erfahrenISO 45001
TermineArbeitssicherheit
Der Standard ISO 45001 beschreibt die Anforderungen an den Gesundheits- und Arbeitsschutz im Unternehmen sowie die entsprechenden Maßnahmen zu ihrer Umsetzung. Dieser Standard ersetzte den bisher weit verbreiteten britischen Standard BS OHSAS 18001 und ist kombinierbar mit anderen Managementsystemen wie der ISO 9001 und der ISO 14001.
mehr erfahrenDIN 77200-1
Sicherheitsdienstleistungen
In der Normenreihe DIN 77200 werden Sicherheitsdienstleistern Hilfsmittel für die Planung und Überwachung an die Hand gegeben, die eine transparente Darstellung der für sie zu erbringenden Sicherheitsdienstleistungen unter Einhaltung festgelegter Kriterien bietet.
Zertifizierungen sind im Moment auf Grundlage des Normteils DIN 77200-1 für folgende Sicherheitsdienstleistungen (SDL) möglich:
1. Stationäre SDL, im Einzelnen:
- Alarmdienst
- Empfangsdienst
- Kontrolldienst
2. Mobile SDL, im Einzelnen:
- Revierdienst
- Interventionsdienst
- Kontrolldienst
3. Veranstaltungssicherungsdienst.
mehr erfahrenUnsere Kunden
Unsere Kunden sind Kleine und Mittlere Unternehmen sowie weltweit tätige Konzerne aus den Bereichen Industrie, Handel und Dienstleistungen sowie Öffentliche Auftraggeber.
Unser Anspruch
Grundlage unserer Leistungen sind motivierte und qualifizierte Mitarbeiter. Diese bilden für uns den Grundstein für die nachhaltige Zusammenarbeit mit unseren Kunden.
Unsere Versprechen
Zertifizierung schafft Vertrauen. Als akkreditierte Konformitätsbewertungsstelle erfolgt die Durchführung unserer Audits unabhängig und neutral auf Basis unserer Akkreditierung sowie der Zufriedenheit unsere Kunden.
Das könnte Sie auch interessieren
Ansprechpartner
Ansprechpartner finden Sie unter dem folgenden Link, aber zusätzlich auch jeweils direkt auf den Seiten zum jeweiligen Standard unter „Zertifizierung“.
mehr erfahrenAngebot anfordern
Haben Sie Interesse an einem Angebot? Bitte rufen Sie uns an oder nutzen Sie das Formular zur Angebotsanforderung über folgenden Link:
mehr erfahren